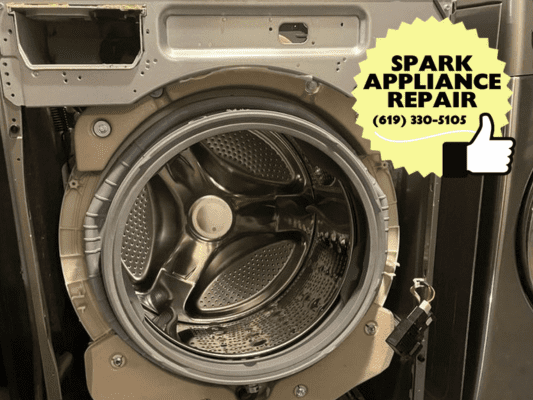
Top 6 Most Common Washing Machine Failures and Repairs
Common washing machine problems plague even the newest high-efficiency models eventually needing diagnosis and repairs for optimal functioning. According to industry experts, the vast majority of washing machine breakdowns stem from recurring electrical, mechanical and leak-related issues with many easy fixes homeowners can tackle themselves. By understanding what causes frequent washer failures plus the DIY and professional solutions available, families can save hundreds maintaining cleaner clothing and linens. This guide covers not only resolving current washing machine problems but also preventing future common breakdowns with proper use and care.
Most Prevalent Washing Machine Problems
Failure to Fill with Water
If laundry isn’t getting adequately soaked and saturated during cycles due to little to no interior water reaching drums, several key components involved in normal fill operations could be malfunctioning. First, inlet valve flaps controlling water flow might be clogged by sediment buildup or stuck in one position unable to toggle open and closed for temporary fills. Plastic supply line hoses wear down overtime developing cracks restricting flow rates to a drip even when valves open on cue. Additionally, control interfaces with digital water level settings can short circuit if connections worked loose not sending electrical signals to other components resulting in zero fills.
Replacing older valves accumulation mineral deposits and restoring constant mechanical flaps rectifies this common issue allowing cycles to fill basins as programmed once more. Inspecting supply lines for subtle cracks followed by replacements also restores water pressure. Technicians can also test control boards and wiring before determining if replacements are necessary to relay intended programming.
Water Leakage
One of the most disruptive common washing machine problems involves water escaping from multiple potential sources. Door seals fabricated with rubber gaskets get rigid and warped over time no longer containing leaks. Drain lines or exterior pump mechanisms face overuse strain ultimately cracking allowing flows outward. Sudden rupture of supply lines from exterior wall fixtures also result in cascading water if hoses lack protective covering.
Examining door seals for deterioration followed promptly by replacements reduces the majority of leakage near openings. Clearing clogged drains then assessing lines and hose cracks points to sections needing polyurethane patched reinforcements or full replacements. Finally, upgraded braided stainless steel hoses prevent supply side ruptures down the road. Taking action to seal vulnerable access points curbs leaks as machines age.
Unusual Noises
While washers operate with low hums and gentle swooshing sounds typically, squeaks, grinding and loud bangs indicate multidimensional problems arising. Drive belts powering interior drum rotation stretch thinner over time, lose elasticity eventually detaching completely throwing off spin capabilities. Unbalanced clothing loads exacerbate side-to-side friction strain. Lubricated drum roller bearings as well as shock absorption components also wear out reducing smooth spin motions cascading into disruptive vibrations.
Begin assessing uncommon sounds by stopping cycles and verifying no stray items like coins causing obvious rattling before reloading evenly. From there loose belts get recoiled towards tension bolts or replaced if worn beyond recoil capabilities while tuning up sticking drum roller bearings realigns spin functionality. Finally technicians can confirm damage to elaborate shock absorbers meant to stabilize spins signaling full replacements necessary to reduce noise through gentle rotations again.
Agitator Failures
Top loading washers utilize central pole agitators descending into filled basins to circulate clothing for optimal cleaning action. Common problems like loose components at agitator bases connecting to shafts leave room for fragmentation throwing off latter stage spin balance once detached. Likewise, worn cogs designed to incrementally rotate agitation direction during wash portions grind down reducing gripping friction. Either issue results in central poles ceasing rotation mid-cycle instead of churning clothing.
Begin by removing fabric remnants or foreign items potentially jamming free clockwise/counterclockwise agitator rotation. Then inspect base connections to its motor verifying bolts sit flush without gaps compromising movement as shafts turn. Consult professional appliances service agents regarding replacing stripped cogs and gears integral to kinetic performance. Finally, avoid overloading drums exaggerating strain on agitators during intense churns.
Control and Display Malfunctions
Modern washing machines depend on intricate computerized controls to select specialized settings from precise wash/rinse temperatures to exact spin sequences, load sizes and more. Blank or frozen digital screens paired with commands failing to start intended activations often stem from feeble circuit board connections. Specifically corrosion slowly impeding transmitting signals often occurs after excess moisture contact from leaks or high humidity laundry rooms.
Tech should begin troubleshooting by examining overall electrical connections first since detached power cables prove a quick fix getting simple commands functional again at low costs. However, corrosion buildup on circuitry may require full control board replacements to maintain responsive mechanical performance based on digital insights. Prevent moisture contact whenever possible by storing washers in climate-controlled spaces without leaks dripping onto sensitive controls underneath.
Spin Cycle Failures
Finally, clean clothing not adequately drying due to failed spin sequences typically involves strain on a select few motorized parts inside drums. Specifically, main drive motors with coils of wiring powering intense rotations wear down over continual use eventually seizing function. Likewise, rubber seals encircling front, main unit openings as well as rear drainage basins degrade over cleaning product contact allowing small fissures water leaks through when spun rapidly. Both gradual issues throw off the stability necessary for uniform high velocity spins.
Professionals can remove drums inspecting motor wiring for visible corrosion confirming replacements. Next, seals receive further scrutiny revealing overlooked cracks behind rigid front facing or rear balance ring locations. If spins still lag after electrical and seal remedies, shock suspension rods, rotational bearings and gear teeth should undergo tune ups given perpetual load strain since more robust enhancements become necessary gradually in any washer. With all said parts optimized across washer brands, rapid spins return properly drying saturated fabric through force rather than solely heated air.
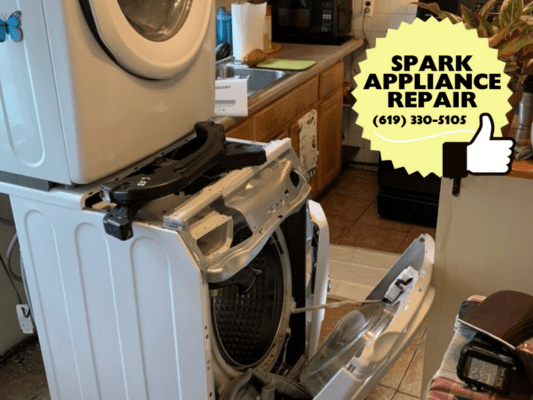
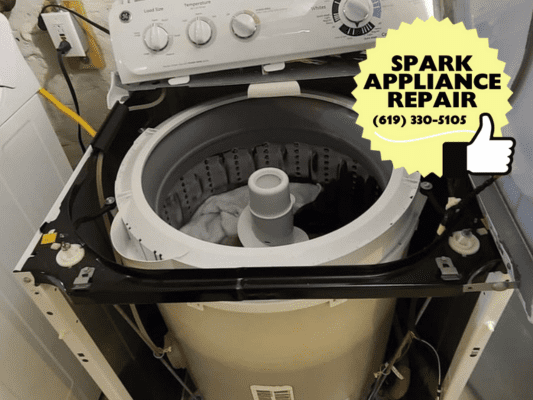
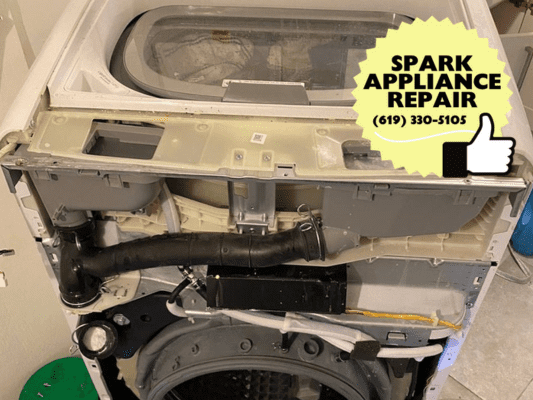
Preventative Maintenance & Early Problem Identification
While certain gradual common washing machine problems manifest despite preventative care, routine maintenance significantly extends machine lifespans delaying breakdowns. Every sixth month, run cleaning cycles on empty at max temperatures ensuring residual buildups get dissolved maintained fresh interiors. Yearly deep cleaning behind drums and door edges clears unseen buildup that impedes mobility. Always leaving lids open after use allows moisture evaporation protecting against corrosion. Lastly, level machines without leaning perpetually taxing certain leak-prone seals during off-balanced spins.
In addition, homeowners can continually stay alert to early stage symptoms. Listen for slight rattling as bearings show initial wear, inspect hoses at bends where cracks start percolating and watch for dripping suggesting gaskets losing elasticity. Catching common washing machine problems early allows simple solutions before catastrophic damage on overloaded parts. Consider yearly tune-ups akin to HVAC maintenance ensuring complexity performs gently over years of Sundays saving households money long term.
When Professional Repair Becomes Necessary
While many common washing machine problems arise from preliminary breakdowns DIYers can tackle with some digital troubleshooting guides, serious structural damage and complex mechanical work requires seasoned appliance professionals.
-
Attempting acrobatics reaching main electrical components past heavy drums risks injury for results probably inadequate anyway lacking proper diagnostic training and tools.
-
Likewise, dismantling gear assemblies in attempts to rebuild intricate kinetic interactions also leave households with lingering issues when improper alignments go overlooked tampering further functionality.
-
Lastly, overlooks like failing to detect very small water leaks behind units continues surrounding floor damage even after obvious cracks get addressed.
Trust certified washing machine technicians for time and cost efficient solutions beyond frustrating uncertainty with risks of safety or consequences from ongoing issues persisting.
Conclusion
Knowing the common problems with washing machines and fixing them early can save money. Instead of buying a new one right away, small repairs can often fix the issue. It’s good to have professionals check the complicated parts, but you can handle basic cleaning and replacing simple parts yourself. Many cities offer rebates for saving energy, so it’s worth it to keep your appliances in good shape. Don’t wait until things get really bad, as small problems can turn into big ones that you can’t fix on your own.
Frequently Asked Questions on Common Washer Problems
This common problem typically stems from an unbalanced load. Clumping weights unevenly strains components and reduces spin speeds. Balancing wash loads evenly prevents this common washing machine failure.
Failing motors burning out windings due to age and overuse is a common problem creating a burning odor during cycles before total breakdown. Early motor replacements prevent this common washing machine problem.
Clogged water supply lines and valves is a common problem reducing rinse efficacy resulting in leftover detergent, especially in older models. Checking both fixes this common issue.
This common problem involves broken shock absorbers resulting in loud rattling from excessive vibrations during wash/spin modes. Replacements halt this noisy common failure.
Worn inner tub seals is a common problem causing gradual leakage exclusively during rapid spins once deterioration allows moisture seepage. Identifying then replacing aged seals prevents this common washing machine issue.